5 Ways Warehouse Management System Increases Supply Chain Resilience
- ERP (Cloud) May 29,2023
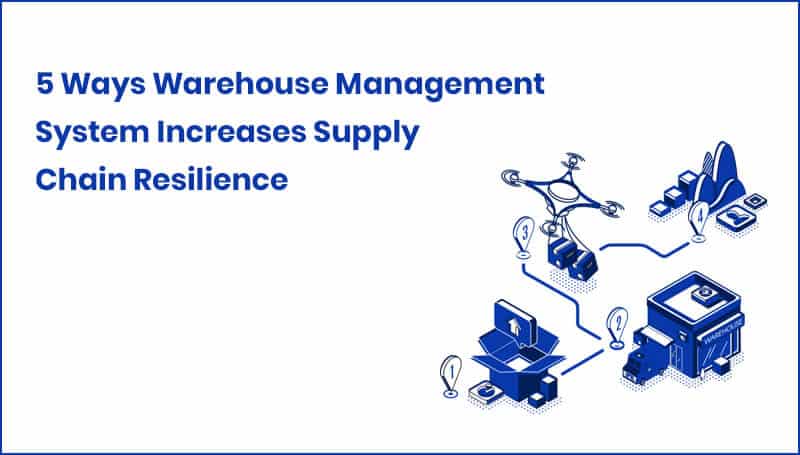
Discover how a Warehouse Management System (WMS) can bolster your supply chain resilience with these 5 effective strategies. Enhance efficiency, visibility, and adaptability for seamless operations.
Between the top of the Second war and therefore, the beginning of the financial crisis in 2008, the United Kingdom saw moderate growth in productivity of around 2% a year. But since 2008, the UK’s productivity has only been growing at an equivalent pace that it had been at before the economic revolution. This marked reduction ranks UK productivity because the worst within the developed world.
One reason productivity is low is because manufacturing companies and distributors are resorting to the utilization of cheap labour to make sure they will get their products out of the door. With rock bottom rates of unemployment for 42 years, UK wages are low at the instant, meaning businesses are willing to spend on payments instead of upgrading their facilities.

But with productivity continuing to flatline, this is often a short-sighted strategy. The sole way that companies are going to be ready to tackle their productivity issues is going to be to deal with their chronic underinvestment in technology, infrastructure and facilities.
Investment in these areas will make the United Kingdom workforce – and therefore, the country’s businesses – more profitable.
There are five areas of importance within the availability chain that companies can specialize in.
Utilize locations
Warehouse “locations” is one among the foremost underutilized principles when it comes to warehouse organization. Locations don’t get the maximum amount attention as they ought to because, quite frankly, they’re taken without any consideration or not acknowledged when it involves warehouse planning.
If you would like to sell more, experience fluid picking and shipping processes, and ultimately reduce labour costs, using “locations” correctly is your initiative.
How nice wouldn’t it be if your pickers could find things in your warehouse? Every item will have a location assigned in the order that they quickly have a reference when it’s time to grab it off the shelf and obtain it out the door.
Generate accurate pick lists
As a fast refresher, “picking” within the warehouse setting refers to the fulfilment process during which an item is chosen, or “picked” from a location then sent off to internal control before shipping to the customer.
A right WMS allows you to get “pick lists” based off of locations. Picklists help your pickers save steps, which successively saves time (and money!).
Hyper Picking may be a method of generating a Wave Picking session but takes it one step further to form your pick process more streamlined. During a traditional warehouse management system using Bins, Wave or Batch Picking usually involves some manual filtering of orders and paper picking of print lists.
With Hyper Picking, SkuVault has eliminated a couple of middleman steps to make a faster and more efficient pick system. Plus, you’ll reduce waste by utilizing digital pick lists. You’ll not only save levels within the warehouse but eliminate the necessity to get paper stock for printing.
Technology Integration
Many warehouse management programs can be integrated into other applications that your company may use, like a business management system or a transportation management system.
For example, one among our retail e-commerce clients has integrated our system with their order (PO) management system. Whenever their customers make a sale from their website, our program is notified then our associates schedule the merchandise for home delivery via parcel service.
At an equivalent time, the WMS system is updated with the parcel tracking number which is then sent to their customer. This example gives their customer the tracking ability that helps foster a positive experience that results in more returning customers.
In the end, our customer is in a position to run their entire e-commerce business from their home without having to stress about processing and storing inventory.
Amp up your internal control
We get it. Your warehouse environment is often quite complex and chaotic. Your pickers are slammed with trying to juggle the pressure of the high season, handling multiple orders simultaneously, and are vulnerable to errors as fatigue starts to line in from long, hectic hours on the ground.
A warehouse management system has vigorous internal control checks in situ, which will highlight exactly where you’re having problems through accurate QC reporting. If you’ve got one particular picker who is continuously pulling incorrect orders, you’ll go straight to the source to correct the behaviour and advance from it.
The very essence of internal control may be a fundamental specialize in customer satisfaction. By now, we all know the importance of delivering the proper item to the customer whenever – once you don’t, it can very quickly negatively affect your seller ratings on sites like Amazon.
One among the best challenges confronting business today is that the continuous increase in customer expectation. Customers are day by day, becoming more critical towards the standard of service they experience.
Have data at your fingertips
Data is arguably one among the foremost vital features of warehouse management software. Employing a WMS should allow you to possess access to a robust arsenal of reports. These reports should offer you access to data which will enable you to form better forecasting decisions for your growing business.
You should easily be ready to see what you’ve got sold, and precisely once you sold it. With an honest WMS, you’ll have visibility into seasonality, so you’ll confirm you’re all stocked abreast of the things you’re selling – not just what you think that you’re.
When it involves increasing efficiency and lowering costs during a warehouse setting, you’ve got to require a strict, honest check out what’s happening in your warehouse. Specialize in what’s happening the minute your inventory arrives in your warehouse until the second that list walks back out the door.
Curious what proportion labour savings your business can experience as a result of streamlining your warehouse processes? Inspect our Labor Savings Calculator and connect your numbers to ascertain for yourself. You’ll be amazed at the quantity of cash you’ll invest back to your business to require things to the subsequent level.