Guide to inventory management and stock Control
- Cloud Based ERP September 11,2023
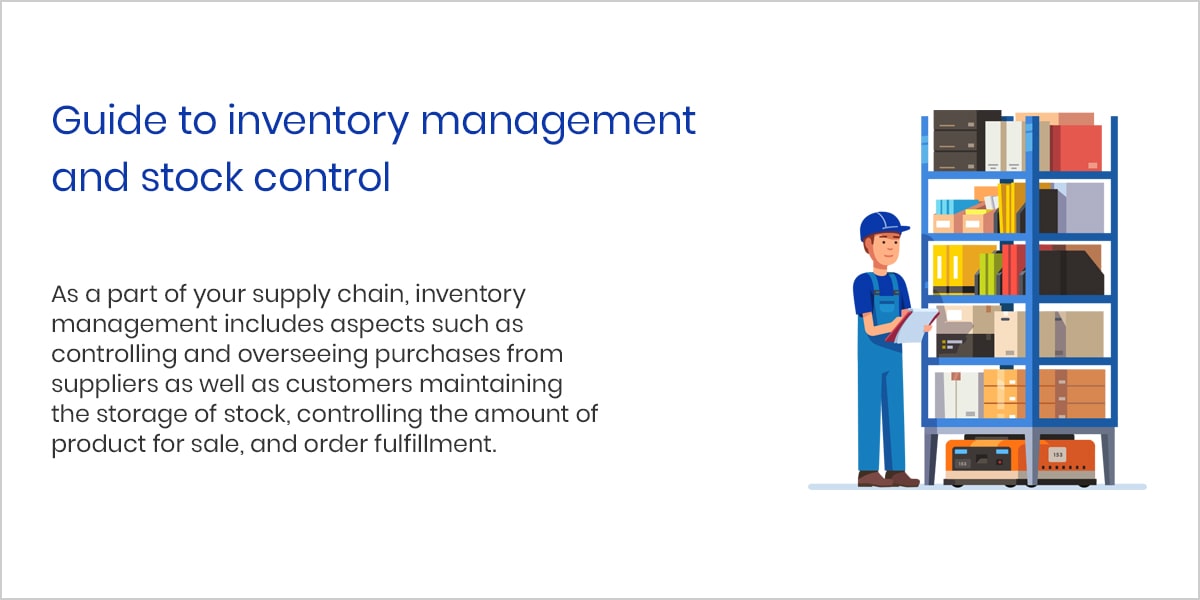
Inventory management is the basis of a well-functioning retail business. Inventory management systems track the lifecycle of inventory and stock because it comes and goes out of your business. Once you don’t skill much inventory you’ve got available, you can’t make smart reorder decisions
You can’t list items accurately online because you don’t have visibility into what proportion inventory you’ve got to allocate to every channel. You grind to a halt with an excessive amount of inventory or an incorrect amount of product. The list is endless.
For any goods-based businesses, the worth of inventory can’t be overstated, which is why inventory management benefits your operational efficiency and longevity.
From SMBs to companies already using enterprise resource planning (ERP), without a sensible approach, you’ll face a military of challenges, including blown-out costs, loss of profits, poor customer service, and even outright failure.

- Reduce costs
- Optimize fulfillment
- Provide better customer service
- Prevent loss from theft, spoilage, and returns
In a broader context, inventory management also provides insights into your financial standing, customer behaviors and preferences, product and business opportunities, future trends, and more.
Which businesses need inventory control?
Any business that handles stock will need internal control of some form. What proportion you’ll need it depends on how important your products are to your business’s success. Any of those businesses will find it absolutely crucial:
- Wholesalers and distributors
- Food/beverage producers, including brewers
- Manufacturers
- Retailers
Inventory control best practice
There’s no single ‘top’ method to regulate your inventory and there are several different approaches and models used. Your best practice will depend upon your business’s unique needs. That said, it’s usually easy to identify the difference between a corporation with optimal control, and one without. Here are three things to aim for:
Set procedures and policy
Perhaps the simplest thanks to achieve an organized warehouse is to select your procedures and policy, then make sure that everyone within the business follows them. As an example, decide what should happen when new stock needs ordering then the way to record it when it arrives.
With all of your staff working in sync, you’ll be ready to reduce wasted stock (say, from breakages or theft), keep one source of inventory information and size up with ease.
Knowing everything that goes out the door
Sometimes products may leave the warehouse without being allocated as a purchase. As an example, your business may sponsor an occasion, donate to a charity, or have some damaged goods from time to time. Companies with sub-optimal internal control often fail to record these departures properly, meaning they find you getting marked as lost goods and final reports are incorrect.
Being proactive
The companies that master internal control tend to possess one thing in common — rather than passively expecting problems to arise, they constantly are careful with improvements they will make to their system. New technologies like RFID or barcode tracking, for instance, can make keeping stock organized much easier by reliably gathering quality data.
Types of inventory
There are many different types of inventory, and which of them you’ll affect depends on the products you sell. Here’s a summary of a number of the kinds you’re more likely to encounter:
- Raw materials: The inventory you employ to form your finished goods
- Work-in-progress: Essentially, unfinished goods — inventory that’s part-way through the manufacturing process
- Safety stock: the extra inventory you retain future to affect supplier shortages or surges in demand
Types of internal control Systems
Inventory control and monitoring systems are accounting approaches to trace the number of products available. The 2 main systems are periodic and perpetual tracking systems.
The Periodic Inventory System
Most small businesses still use periodic inventory management because it doesn’t require sophisticated software or inventory scanning.
A periodic inventory system relies upon occasional or regular physical counts of the inventory. You opt accounting periods supported the business needs, but you don’t track inventory daily or continuously. Instead, you record all purchases to a sale account.
Once you conduct the physical inventory, you shift the balance within the purchase account into the inventory account. Finally, you adjust the inventory account to match the value of the ending stock. You’ll calculate the value of ending inventory using either FIFO (first in, first out) or LIFO (last in, first out).
The challenges of the periodic system are especially apparent when performing a physical inventory count. Most conventional business activities must be suspended during this point because it requires significant manual labor.
Many companies hire additional staff and check out to perform this outside of normal business hours, like during an evening shift. This sort of system incurs more fraud because there’s nothing tracking inventory between physical counts, reducing accountability between inventories, and since it’s tougher to work out where any inventory discrepancies occurred.
The Perpetual Inventory System
The perpetual system could also be costlier to implement than the periodic system thanks to equipment and software needs. This technique calculates inventory supported sales and purchases via the purpose of sale and asset management software.
This way, you’ve got accurate stock on-hand accounting in the least times. Perpetual tracking is that the best thanks to avoid stock outs when your customers deplete inventory on a specific product. With a perpetual system, you’ll achieve minimal employee contact with the products.
The challenges of this sort of system occur once you use it without also performing physical inventories. In other words, the recorded inventory might not accurately reflect what in-stock is physically as time goes by, never mind accounting for drop shipments or inventory on order.
You want to account for breakage, stolen goods and loss to make sure the system is accurate. Further, errors and improperly scanned items affect the inventory records. You’ll handle this mathematically by applying corrections that mostly account for this stuff.
Experts agree, though, that albeit physical inventories aren’t common, you ought to implement some manual stock taking process to enrich a perpetual system. You’ll integrate these sorts of systems with supply-chain automation to form quicker decisions informed by data.